Inventa has successfully developed an innovative filtration technology, which allows filtration temperatures of up to 300 °C. Furthermore, no pre-coating of the filter elements is required. The Inventa Hot Filtration Technology can be applied to batch or continuous plant operation and can be operated fully automatic without manual operator intervention.
Filtration reinvented
Filtration reinvented
Clean Tech
Our commitment towards green chemistry starts with our feedstock and the plant design and ranges all the way through to the final product. At Circular Industries we have developed and implemented technologies and processes that minimize emissions and the required inputs while maximizing output.
Biofacturing
At Circular Industries we rely on bio-waste material as feedstocks and use environmentally friendly and nature driven biochemical processes to generate high-margin products.
cGMP Standards
Quality, consistency and safety are Circular Industries’ top priorities and we are hence always adhering to the current Good Manufacturing Process standards (cGMP).
Focus on Quality
Circular Industries’ customers expect superior quality of our premium products. it is our goal to exceed these expectations.
catalyst recovery and recycling

Chemical processes often require heterogeneous catalysts. The catalyst recovery has traditionally been done by plate and frame or pressure leaf filters. Inventa’s filtration technology utilizes sintered metal filter elements and provides far more superior performance.
Inventa’s sintered metal filtration technology has been successfully applied for the removal and recycling of precious metal catalysts and other catalyst types in the pharmaceutical, specialty chemical and food industry.
Catalyst Type
- Raney Nickel Nickel catalyst
- Palladium catalyst
- Rhodium catalyst
- Copper catalyst Platinum catalyst
- etc.
The Inventa catalyst separation technology allows for an automatic recycling of catalyst into the reactor or an automatic discharge into a spent drum for re-processing. A special heel filter will allow for dry catalyst discharge. Filter elements are easily freed of catalyst cake by using gas or liquid discharge methods and there are no requirements for scrubbing, scraping or rotating filter elements. Contaminants may also be removed with water, steam, nitrogen, solvents, alkaline or acidic washing or ultrasonic. As the sintered metal filter does not require any pre-coating or filter aid, the catalyst is less contaminated and facilitates recycling or metal recovery from spent catalyst.
bleaching earth filtration

Chemical processes often require heterogeneous catalysts. The catalyst recovery has traditionally been done by plate and frame or pressure leaf filters. Inventa’s filtration technology utilizes sintered metal filter elements and provides far more superior performance.
Inventa’s sintered metal filtration technology has been successfully applied for the removal of spent bleaching earth of adoption agents in functional food, specialty chemicals and oleochemical industry.
Catalyst Type
- Raney Nickel Nickel catalyst
- Palladium catalyst
- Rhodium catalyst
- Copper catalyst Platinum catalyst
- etc.
The Inventa catalyst separation technology allows for an automatic recycling of catalyst into the reactor or an automatic discharge into a spent drum for re-processing. A special heel filter will allow for dry catalyst discharge. Filter elements are easily freed of catalyst cake by using gas or liquid discharge methods and there are no requirements for scrubbing, scraping or rotating filter elements. Contaminants may also be removed with water, steam, nitrogen, solvents, alkaline or acidic washing or ultrasonic. As the sintered metal filter does not require any pre-coating or filter aid, the catalyst is less contaminated and facilitates recycling or metal recovery from spent catalyst.
fully automated filtration operation
Circular Industries’ decentralised biofacturing hubs are designed to create synergistic local islands of biofacturing. Its highly integrated infrastructure and operational units are in harmony with nature and deploy most advanced energy material recovery systems. Its proximity to local markets connects both customers and suppliers delivering a minimum carbon foot print for logistics. These integrated facilities deliver benefits that allow companies to save costs.
artificial intelligence controlled filtration process
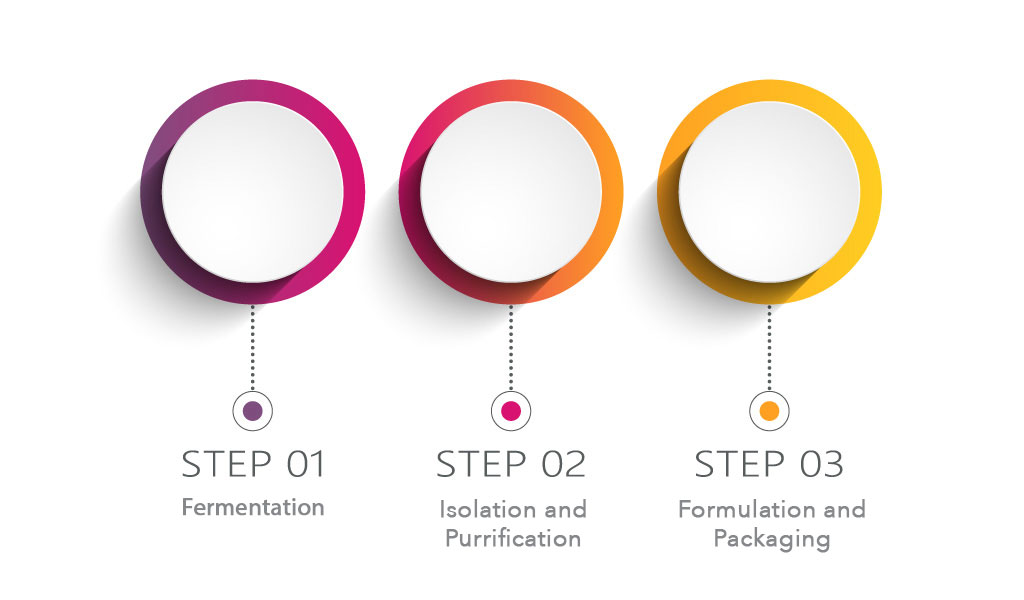
Circular Industries has developed a fully automated and continuous production process that ensures an efficient, consistent as well as safe manufacturing cycle.
The manufacturing cycle starts with the fermentation of waste material into intermediary substances. From there the substances automatically enter an isolation and purification step, followed directly by the final formulation and packaging step. The whole cycle is continuously overseen by adequate sensors, systems and our experts to ensure consistency, quality and safety of the end product.
effective
Circular Industries is taking action against global warming. Our scientists believe in effective and lasting innovation. The minds of an interdisciplinary team delivered solutions which will disrupt and serve as a game changer in the field of natural waste stream utilisation. Our technology is effective in addressing environmental challenges and delivering commercially viable options in line with modern and futuristic trends.
innovative
Innovation and the use of technologies like Artificial Intelligence (AI), machine learning, Internet of Things (IoT) , big data analytics and mobility are changing processes and business models across all industry verticals and the chemicals and bio-tech industries are no exceptions. Circular Industries applies innovation in the bio-technology complexes from the early stage of raw material sourcing to to the final stage of end-product distribution.
smart
Significant time and resources went into the development of biotechnology inventions. Circular Industries is taking the next step in the commercialisation of smart solutions. Starting with the collection of waste products from the food industry to the impact of a major CO2 footprint reduction, the team is dedicated to apply smart solutions to its innovative business.